Understanding the Role of Plastic Injection Mould Manufacturers
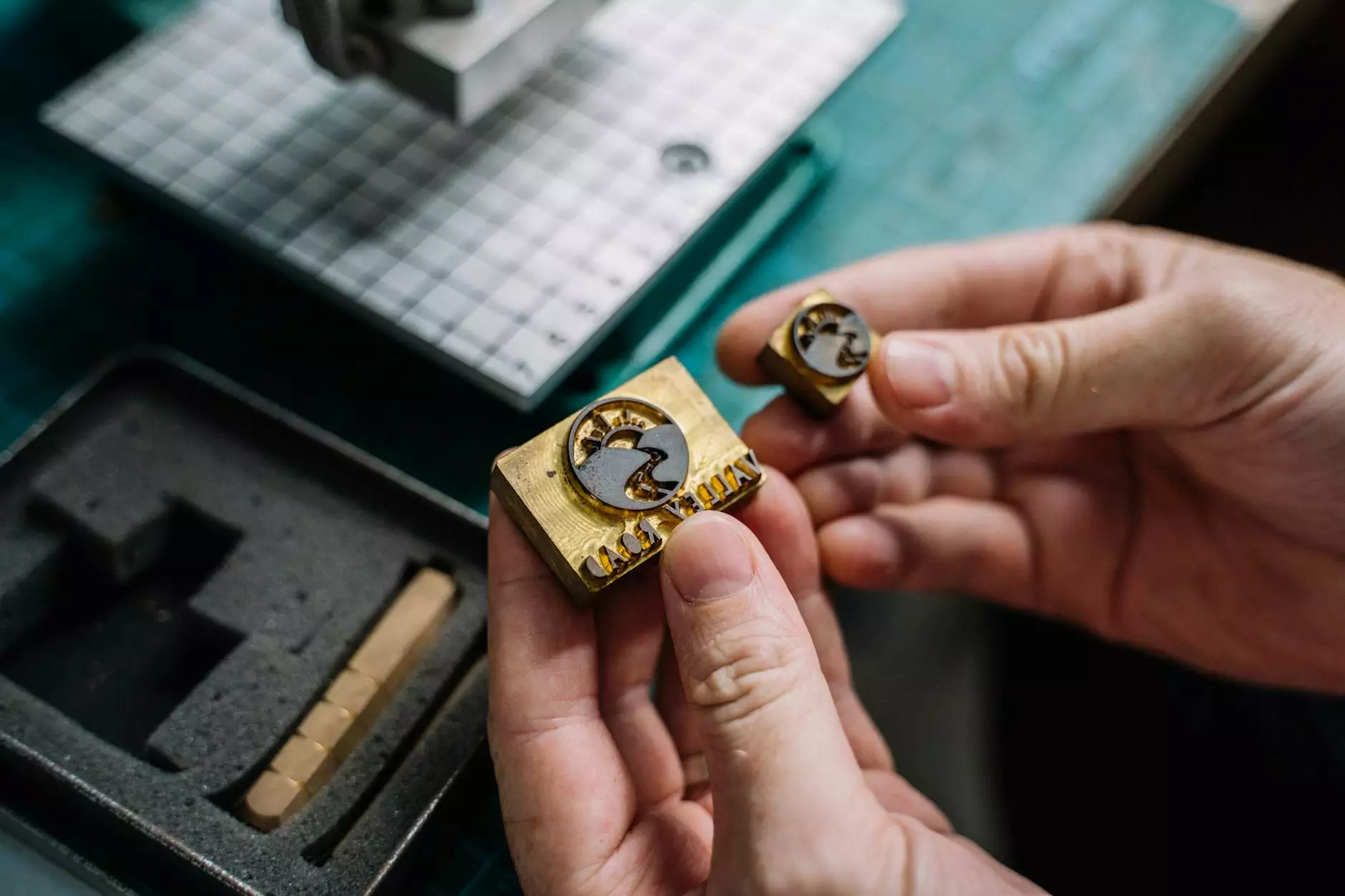
Plastic injection mould manufacturing is a critical process that serves as the backbone of various industries, including automotive, consumer goods, and electronics. As we delve into this topic, we will explore the intricacies of this manufacturing process, its benefits, and the factors that contribute to its effectiveness. Our goal is to provide you with comprehensive insights that will help you understand why plastic injection mould manufacturers like those at Deepmould.net are essential to modern production capabilities.
The Process of Plastic Injection Moulding
The essence of plastic injection mould manufacturing lies in its innovative process. Here’s how it works:
1. Material Selection
One of the first steps in the plastic injection moulding process is selecting the right plastic material. Common options include:
- Polyethylene (PE)
- Polypropylene (PP)
- Polystyrene (PS)
- Polyvinyl Chloride (PVC)
- Thermoplastic Elastomers (TPE)
Each of these materials has unique properties that make them suitable for various applications. For instance, PP is known for its lightweight and chemical-resistant features, making it ideal for automotive parts.
2. Mould Design
Once the material is chosen, the next step is to create a mould design. This is a crucial phase where engineers must consider several factors:
- Complexity of the part
- Required tolerances
- Production volume
- Material flow
A well-designed mould will facilitate easier production and result in higher-quality parts, reducing scrap rates and production costs.
3. Injection of Material
The core of the plastic injection moulding process involves heating the plastic until it reaches a molten state and injecting it into the mould under high pressure. This ensures that the material completely fills the mould cavity, capturing all intricate details of the part design.
4. Cooling and Solidification
After injection, the molten plastic needs to cool and solidify. This is a critical phase where the temperature of the mould is carefully controlled to achieve the desired dimensional and mechanical properties of the finished product.
5. Ejection and Finishing
Once cooled, the mould opens, and the final product is ejected. At this stage, finishing processes such as trimming, sanding, or painting may be applied to enhance the final appearance and function of the part.
Advantages of Plastic Injection Moulding
Plastic injection moulding offers numerous advantages that make it a preferred choice for manufacturers:
1. High Efficiency and Speed
The plastic injection moulding process is known for its high efficiency. Once the moulds are made, parts can be produced rapidly, significantly speeding up the production timeline.
2. Consistency and Precision
Injection moulding produces parts with excellent consistency and precision. Each part produced in a cycle is nearly identical, ensuring uniform quality across large production runs.
3. Complex Geometries
With advanced mould designs, manufacturers can create complex shapes and intricate designs that would be impossible to achieve with other manufacturing techniques.
4. Material Versatility
There are numerous types of plastics that can be used in injection moulding, allowing manufacturers to choose materials that best fit their specific application needs.
5. Reduced Waste
Injection moulding is a highly efficient process that minimizes waste by using only the necessary amount of plastic material, making it more environmentally friendly compared to other manufacturing processes.