The Importance of Die Casting Injection Molding in Modern Manufacturing
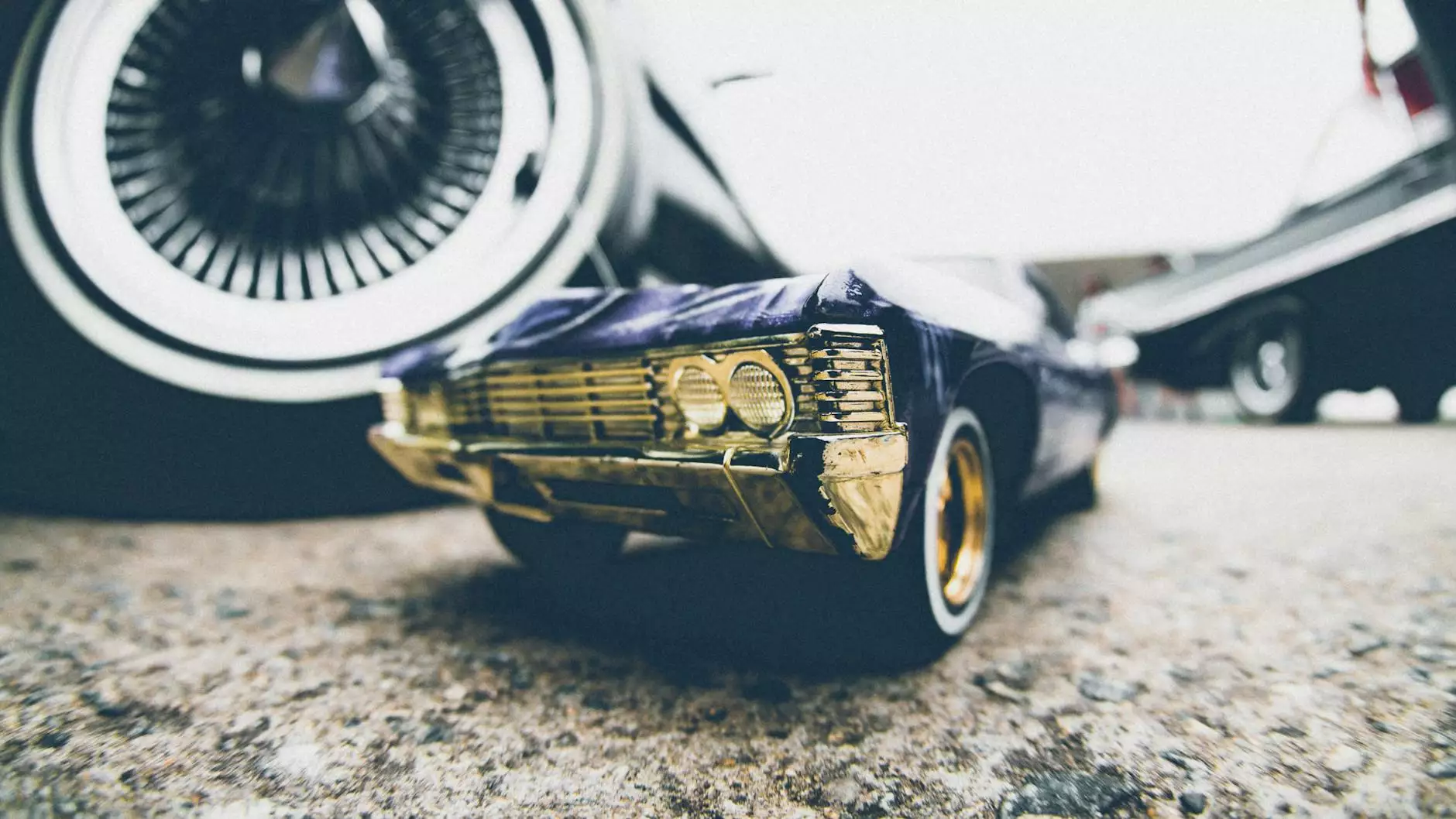
In the rapidly evolving world of manufacturing, die casting injection molding stands out as a premier technique utilized in various industrial applications. This method is pivotal for producing high-quality metal components that meet the stringent quality standards required in today’s competitive market. This article delves deep into the definitions, processes, advantages, applications, and future of die casting injection molding, emphasizing its role in the metal fabrication industry.
Understanding Die Casting Injection Molding
Die casting injection molding is a process in which molten metal is injected into a mold cavity to create parts. This process is characterized by the high pressure used to force the molten metal into the mold, allowing for the production of complex shapes with exceptional precision. The metals commonly used in this process include zinc, aluminum, and magnesium, which allow for the creation of lightweight yet robust components.
Key Components of the Process
To better understand die casting injection molding, let’s break down the key components involved in the process:
- Melted Metal: The starting material, typically a metal alloy, is heated until it becomes liquid.
- Molding Die: Two halves of a steel mold that define the part’s geometry.
- Injection Mechanism: The equipment used to inject the molten metal into the mold at high pressure.
- Cooling System: Intercooling systems help solidify the part quickly, allowing for efficient production cycles.
- Part Ejection System: Devices that remove the finished part from the mold, minimizing damage and wear.
Advantages of Die Casting Injection Molding
The adoption of die casting injection molding is driven by its numerous advantages, appealing to manufacturers across various sectors. Some of the key benefits include:
- High Precision and Tolerance: The process ensures tight tolerances, making it ideal for applications that require exact specifications.
- Efficiency in Production: With cycle times as short as 15 to 60 seconds, manufacturers can produce vast quantities of parts quickly.
- Cost-Effectiveness: Despite initial tooling costs, the high volume production and reduced waste lead to lower overall costs per unit.
- Complex Geometries: The ability to produce intricate designs opens up new possibilities for innovation and product development.
- Material Versatility: Different alloys can be used, offering flexibility in mechanical properties tailored to specific applications.
Applications of Die Casting Injection Molding
Various industries utilize die casting injection molding for creating components ranging from automotive to aerospace, and consumer electronics. Below are some specific applications:
1. Automotive Industry
The automotive industry is a significant consumer of die casted components. Parts such as engine blocks, transmission cases, and structural elements benefit from the lightweight and strong characteristics of die-cast metals. The demand for efficiency and fuel economy in vehicles has driven manufacturers to incorporate more die-cast components into their designs.
2. Aerospace Industry
Aerospace applications require materials that are not only lightweight but also incredibly strong and durable. Components such as housings, brackets, and structural supports often utilize die cast techniques. These parts must withstand extreme conditions, making die casting essential for safety and performance.
3. Consumer Electronics
Consumer electronics benefit from the complexity and precision offered by die casting injection molding. Components such as housings for smartphones, laptops, and other electronic devices require both aesthetics and durability, which die casting can deliver effectively.
4. Industrial Equipment
The manufacturing of industrial machinery often involves the use of die-cast parts. Gear housings, pump bodies, and other critical components are fabricated using this process, ensuring reliability and performance under heavy loads.
Challenges in Die Casting Injection Molding
While die casting injection molding offers an array of benefits, it is not without challenges. Some of the issues manufacturers may face include:
- Tooling Costs: Initial setup and tooling can be expensive, particularly for smaller production runs.
- Design Limitations: There are limitations on wall thickness and detail that must be considered during design.
- Defects in Parts: Issues such as gas porosity or incomplete filling can occur if the process is not properly managed.
The Future of Die Casting Injection Molding
As technology continues to evolve, the future of die casting injection molding looks promising. Innovations in materials, design, and automation are set to enhance efficiency and expand the application of this technique. Here are some future trends to watch:
- Automation and Industry 4.0: The introduction of smart manufacturing processes will enable real-time monitoring and adjustments to improve production efficiency.
- Advanced Simulation Software: Investment in modeling software will lead to better design processes and troubleshooting capabilities, reducing defects.
- Sustainability Practices: As industries move towards sustainable practices, die casting processes are being optimized for energy efficiency and reduced material waste.
- Hybrid Manufacturing: The combination of die casting with additive manufacturing techniques may lead to enhanced capabilities in production.
Choosing the Right Partner for Die Casting Injection Molding
As a business seeking to implement die casting injection molding, selecting the right manufacturing partner is crucial to your success. Consider the following factors:
- Experience and Expertise: Look for a partner with extensive experience in die casting processes and metal fabrication.
- Quality Standards: Ensure that they adhere to rigorous quality control measures and hold necessary certifications.
- Technical Capabilities: Verify that they have the latest technology and equipment to meet your production needs.
- Customer Support: A partner who offers excellent support and communication can help navigate challenges as they arise.
- Flexibility: Assess their ability to adapt to changes in demand or project specifications quickly.
Conclusion
In summary, die casting injection molding is a fundamental process in modern manufacturing, offering remarkable benefits in terms of precision, efficiency, and versatility. As industries continue to evolve, this method will undoubtedly play a crucial role in shaping the future of metal fabrication. By understanding the intricacies and advantages of die casting, businesses can leverage this process to enhance production quality and drive innovation. At DeepMould.net, we are committed to providing unparalleled services in die casting injection molding, catering to the specific needs of our clients across various industries.
For more information on our services or to discuss your project requirements, please visit our website at DeepMould.net and discover how we can help you achieve your manufacturing goals.